Ellenex Conformal Coated Electronic Parts, A Difference That Matters
- Savio Navaratne
- Sep 7, 2023
- 4 min read

Introduction: A Splash of Science in the Tech Universe
Picture this: an intergalactic dance of tiny electrons, zipping and zapping through intricate circuits, powering the gadgets that light up our lives. But what if I told you that there's more to this electronic symphony than what meets the eye? Enter the mysterious realm of conformal-coated electronic parts – the unsung heroes of durability and resilience in the tech world. Buckle up as we embark on a journey to unravel the magic behind these hidden wonders!
Chapter 1: Cracking Open the Coating Conundrum
Imagine your smartphone as a fearless explorer, navigating a world of liquids, dust, and cosmic chaos. How does it brave this unpredictable environment without short-circuiting? The answer lies in conformal coating. Think of it as a superhero suit for your gadgets – a thin protective layer that shields delicate electronic components from the harsh elements they encounter.
Conformal coating is like a protective skin made of a thin plastic-like material that's put on printed circuit boards (PCBs). It's called "conformal" because it fits the shape of the PCB. This coating helps shield the PCB from things like water, dust, chemicals, and extreme temperatures. Nowadays, it's even used to stop tiny wire-like growths (called whiskers) and prevent current bleed between parts that are positioned next to each other.
Chapter 2: From Humble Beginnings to High-Tech Guardians
The history of conformal coating takes us back to the mid-20th century when engineers were already dreaming of waterproof gadgets. Early attempts involved dipping entire assemblies into protective substances like wax or oil – a bit like giving your phone a bubble bath! Thankfully, technology evolved, and now we have specialized coatings made from materials like silicone, acrylic, polyurethane, and even parylene (a super-thin polymer).
Chapter 3: The Fabulous Five; Types of Conformal Coatings
Silicone Shield
Like a second skin, silicone coatings offer fantastic protection against moisture and temperature extremes. They’re flexible, durable, and even provide a level of vibration dampening. Just like a chameleon, they adapt to their surroundings.
Acrylic Armour
If your gadget were a medieval knight, acrylic coatings would be its chainmail. Transparent, easy to apply, and resistant to fungi, they guard against moisture and dirt, while letting you admire the delicate circuitry within.
Urethane Umbrella
When it's raining uncertainty, polyurethane coatings act as the trusty umbrella. They’re tough, chemical-resistant, and can endure outdoor escapades without flinching.
Parylene Prestige
Imagine wrapping your gadget in an invisibility cloak – that's parylene for you. This vapour-deposited polymer seeps into every nook and cranny, forming a pinhole-free shield against moisture and chemicals.
Epoxy Enchantment
If gadgets went to a magic school, epoxy coatings would be the protective spells. They offer superb chemical resistance, durability, and electrical insulation – a true all-rounder.
Chapter 4: The Top-Secret Application Process
So, how do engineers coat electronic parts without turning them into a gooey mess? It’s a delicate dance of precision! Picture a lab where skilled technicians apply coatings using methods like brushing, spraying, or dipping. The secret lies in controlling factors like viscosity, temperature, and curing time. It's like cooking up a masterpiece, but instead of a meal, you're serving up a safeguard for your tech treasures.
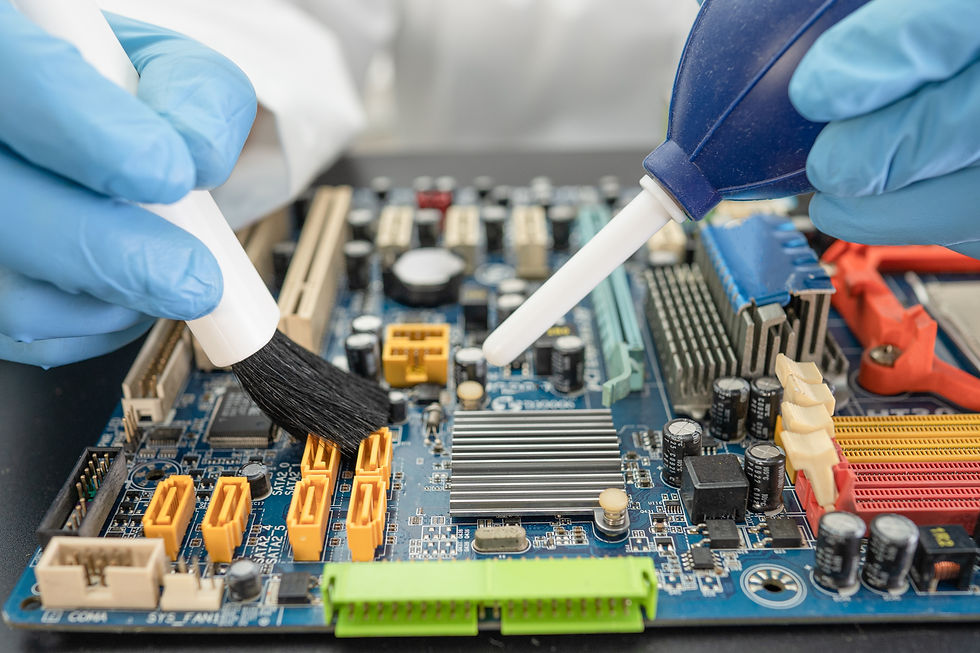
Chapter 5: The Power of Invisibility; Benefits Galore
Moisture Repellent Magic: Like a superhero deflecting bullets, conformal coatings repel moisture, ensuring your gadgets work even in the most humid of jungles or the rainiest of days.
Dust-Proof Charm: Just as Cinderella's glass slipper protected her foot, these coatings shield against dust, preventing it from clogging sensitive electronic components.
Chemical-Resistant Enchantment: Spills and splashes are no match for these coatings, which laugh in the face of chemicals that might otherwise corrode your beloved gadgets.
Temperature Tolerance Trick: From the hottest deserts to the coldest tundras, conformal coatings ensure your gadgets won't break a sweat (or freeze their circuits).
Based on a study conducted by Fortune Business Insights, the global market size for conformal coatings was valued at USD 899.1 million in 2021, anticipating a CAGR of 5.8% from 2022 to 2029, facilitating an increase from USD 940.8 million (2022) to USD 1392.8 million (2029). Furthermore, this growth study was based on their use in various automotive, consumer electronics, medical and aerospace & defence applications.
Chapter 6: The Dark Side; Drawbacks to Consider
While the world of conformal coated electronic parts seems like a realm of magic and protection, every enchanted tale has its darker side. Amidst the glimmering benefits, there are some shadows to be aware of. So, let’s venture into the land of cautious considerations:
Rework and Repair Difficulty
Once a component dons its conformal coat, making changes becomes a puzzle. Removing the coating requires the skill of a master magician, as even a small misstep can lead to delicate components becoming collateral damage.
Coating Conundrum
Like a fairy-tale spell gone wrong, improper application can lead to uneven coverage, air bubbles, and gaps in the coating’s shield. This could expose your gadget’s innards to danger, rendering the coating’s protection ineffective.
Heat Hurdle
While these coatings are protective capes, they can also be insulating blankets. Trapped heat can turn your gadget into a hot potato, potentially affecting its performance and lifespan.
Contaminant Confinement
Like an overenthusiastic castle moat, these coatings can inadvertently trap moisture and particles, leading to slow but steady corrosion and wear over time.
Elusive Accessibility
Coated components can play hard to get, especially during testing, troubleshooting, or inspection. It’s like trying to find a needle in a haystack, but the needle is wearing a cloak of invisibility.
Electricity’s Quandary
Some coatings have a quirky relationship with electricity, which might affect signals or electromagnetic interference (EMI) shielding. Picking the right coating is like choosing a dance partner with matching steps.
Costly Conjuring
Just like a grand magical show, applying conformal coatings comes with its price tag. Equipment, materials, and labour costs can pile up, adding a little extra to your tech investment.
Compatibility Spells Trouble
Not all components are fans of these coatings. Some might have an allergic reaction to the chemicals, leading to unexpected issues.
Thickness Tango
Achieving a consistent and effective coating thickness can be as tricky as teaching a dragon to play the flute. Variations in thickness can turn the coat from armour to a mere accessory.
Time-Twisting Delays
As enchanting as the process may sound, coating electronic parts can be as time-consuming as a magical ritual. This can slow down production timelines, leading to impatient customers.
Regulatory Runes
Different lands have different rules, and the same applies to coatings. Some regions or industries have standards about which chemicals can be used, adding an extra layer of complexity to the mix.
The top 5 vendors in conformal coating of electronics: Chase Corporation, Dow Corning, Henkel, Plasma Ruggedised Solutions, and VSI Parylene. ~By Business Wire.

Chapter 7: The Book of Potions: Regulations & Standards
IPC-CC-830C: Imagine IPC-CC-830C as the grand tome of all things conformal coating. This is the foremost standard that sets the stage for the enchantment to unfold. It stands as the guardian, qualifying different conformal coating products and revealing the secrets of materials, shelf life, curing, chemical properties, viscosity, and appearance requirements. It's a treasure chest of wisdom that even covers resistance against the mischievous fungus, moisture, and flames, along with vital electrical specifications like dielectric withstanding voltage.
IPC-A-610G: In the realm of electronic assemblies, IPC-A-610G is the spell book that defines what's acceptable and what's not. It dedicates a section to the art of conformal coating, specifically addressing coverage and thickness. Just as knights must wear their armor flawlessly, electronics assemblies must wear their coatings with precision, and this standard ensures they do just that. An example of ideal liquid conformal coating thickness values is:
Material | Thickness values |
Acrylic | 30-130 µm |
Polyurethane | 30-130 µm |
Silicone | 50-210 µm |
IPC J-STD001F: Picture IPC J-STD001F as a potion that brews the perfect soldered assemblies. While it may seem distant from coatings, it still has a section that deals with materials and application of conformal coatings. Just as a potion's ingredients must be mixed perfectly, the application of coatings requires meticulous attention to detail to ensure the final enchantment is flawless.
Chapter 8: Alchemy at Ellenex; How Conformal Coated Electronic Parts Impact Ellenex
Let’s turn our gaze inward and explore how this magical technology affects our company and its endeavours. Just as knights must adapt to the landscapes they traverse, so must we adapt to the advantages and challenges that these coatings bring.
Enhancing Durability and Reliability
By incorporating these coatings into our electronic parts, we bolster the longevity and reliability of our offerings, fostering customer trust and loyalty.
Elevating Brand Reputation
A company's reputation is its most treasured possession, akin to a dragon's hoard. By utilising conformal-coated electronic parts, we showcase our commitment to quality and reliability. Customers are more likely to view our products as technologically advanced and forward-thinking, which can elevate our brand's standing in the competitive market.
Mitigating Potential Drawbacks
Every adventure has its pitfalls, and the world of conformal coatings is no exception. By being aware of the drawbacks outlined earlier, we can prepare strategies to address and minimize them. This proactive approach ensures smoother production processes, reduces downtime due to repairs, and keeps costs within manageable bounds.
Tailoring Solutions to Industry Needs
Just as every knight possesses unique skills, each industry has distinct requirements. Whether we're in the automotive, aerospace, or medical sector, understanding how conformal coatings align with industry standards and regulations is crucial. Adapting our offerings to meet these requirements positions us as a reliable partner for specialised needs.
Balancing Cost and Benefit
Every quest requires resources, and incorporating conformal coatings is no different. While the application process adds to production costs, the benefits in terms of durability and customer satisfaction may well outweigh the investment. Striking the right balance between cost and benefit is a strategic feat that positions Ellenex for long-term success.
Embracing Innovation and Adaptability
By embracing conformal coatings, we showcase our ability to adapt to emerging trends and technologies. This positions us as a cutting-edge player, capable of harnessing innovation to deliver superior products.
Collaborative Partnerships
Just as companions join forces on a quest, our company may need to form partnerships with coating material suppliers, equipment manufacturers, and industry experts. These collaborations ensure that we access the latest advancements and insights in the realm of conformal coatings, enhancing our overall capabilities.
Customer-Centric Approach
The heart of any quest lies in serving the needs of those we aim to protect. By integrating conformal coatings, we offer customers products that endure and perform admirably. This customer-centric approach not only boosts sales but also establishes a bond of trust between our company and its clientele.
The world of conformal coated electronic parts is a landscape filled with both promise and challenges. As Ellenex sets forth on this journey, let us remember that every adventure requires courage, adaptability, and a dash of wizardry. By carefully considering the impact of conformal coatings on our products, brand reputation, and customer satisfaction, we at Ellenex, chart a course that leads to a brighter, more resilient future for our company and its offerings.
Conclusion: The Enchanted World of Conformal Coatings
In a world where gadgets are the real-life magic wands that shape our reality, it's easy to overlook the unsung heroes that keep them alive and kicking. It’s important to peer beyond the surface and understand the drawbacks alongside the benefits.
By weaving the previously discussed standards into our process, we align our efforts with the entire magical community of electronics manufacturing, setting a benchmark for excellence in the world of conformal-coated electronic parts. Conformal coatings, with their protective prowess, are the wizards safeguarding our electronic kingdom. So, next time you reach for your phone or flip open your laptop, take a moment to appreciate the invisible cloak of resilience that allows them to work their enchantment in our lives!